Working
The Concrete
Batching
By Volume
Batching
is the process of measuring out the
materials per load as accurately
as possible. On small projects batching
is normally carried out by
volume.
Where
mixing is by hand, batches should be
based on whole bags
of cement, using the amounts of sand and
stone as given in
Tables 1 or 2 of page Estimating
& Ordering Materials
for different stone sizes.
Tip:
Where
mixing by hand
is unavoidable, use smaller sized stone,
e.g.13,2
mm
instead of 19 mm if at all possible as
hand mixing concrete is very hard
physical labour.
Note:
A
bag of cement contains 50 kg of cement,
or approximately 33 litres. It is recommended
that only whole bags be
used, as cement "fluffs up"
when poured
into another container.
Volume
batching of
sand
can never be precise
because
the
quantity (mass)
of
sand
in a container varies with the moisture
content of
the
sand, and with the
degree to which it is compacted
in the
container.
Tip:
Don't
mix concrete directly on ground:
-
The
ground absorbs mixing water from the
fresh mix,
affecting workability and potential
strength, and
-
The
mix will become contaminated with
soil.
Work
on a clean, hard surface such as a
concrete floor
or a metal sheet. Very small
batches can be mixed
in the wheelbarrow.
First
spread out the measured materials in
even layers.
Mix the materials with a spade or shovel
until
no gray streaks are seen, then make a heap
and hollow out the middle. Next, pour some
of the water slowly into the hollow and shovel
material from the edges of the heap into
the centre, turning over
each shovelful as it is dumped.
Add
a little more water at a time while
turning the material over, shovelling
from the centre to the side and back to
the centre of the heap, until the whole
batch is the same colour and
consistency.
Machine
mixing
For
machine mixing, the amount of
cement, stone, sand and water
in each load should be just enough
to allow the mixer to
mix efficiently. Use the yield
given in Table 1 or 2
to calculate the correct
volume of each raw material per
load.
Don't
overload or underload the mixer
drum. If
the
mixer capacity is given by two
numbers,
the
second figure is the yield or volume
of
wet
concrete that can be mixed efficiently,
e.g. a mixer rated 150/100 has
a maximum output
of
100 litres.
If
mixer
capacity
is given by only one number,
this
is the yield in litres.
|
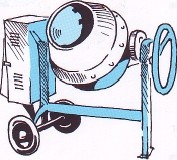
|
When
loading directly into the mixer from
barrows, buckets, etc,
load the stone first, together with some
of the water to clean
the drum and prevent build-up of mortar
around the blades.
Load the cement next, followed by the
sand and the remaining water.
Mixing
time must be long enough to
produce concrete of uniform colour and consistency
-
usually
between two and three minutes.
(Inadequate
mixing
leads to colour differences,
variable
strengths and
lack of
durability.)
Ready-mixed
concrete
Ready-mixed
concrete offers a speedy, cost-effective
alternative to site batching. When
calculating relative costs, take into account
the total cost of the materials delivered
to site, storage, wastage and theft,
the hiring or purchasing and operating
costs of the necessary plant, as well as
the cost of labour and supervision.
There
are many benefits in ordering concrete
from a readymix supplier,
especially when larger volumes are
required. Here
are a few:
-
The
readymix supplier has the resources
and the technical expertise to
provide a range of mixes, matching the
right mix design to the application
-
The
quality of the concrete is guaranteed.
Site batching tends to have a higher
risk of strength variability
due to the lack of sophistication
of small batching plants
-
Concrete
can be ordered to fit in with the
total construction programme,
and delivery times can be changed at
reasonably short
notice, e.g. to avoid placing in bad
weather
-
One
load of ready-mixed concrete can be
discharged directly to
several positions on site, saving
time and labour moving concrete
in wheelbarrows
-
Discharge
from a readymix truck is faster than
from wheelbarrows
-
Site
batching in residential areas raises
concerns about noise levels
and duration, messing of
frontages/verges and potential contamination
of stormwater drains
-
No
storage of materials on site means
less pilferage, and no environmental
concerns - and
no clean-up operations after construction
-
Most
readymix suppliers also offer a
pumping service. Where access
is difficult, pumping moves concrete
quickly across distances
and heights that would otherwise be
problematic. This helps one avoid the
concrete to segregate, lose fine
material, dry
out or become diluted or
contaminated.
Tips
-
When
using ready-mixed concrete make sure
that access to the site is clear,
that the roadway is strong enough to
support the
weight of the full mixer truck and
that the truck
will be able to safely discharge
concrete as
close as possible to where it is
required.
-
Prior
to mixing or ordering concrete,
check that the foundations
have been excavated to the correct
depth and
width
and that any
required formwork and/ or
reinforcement is in place.
-
If
there is steel reinforcement
involved ensure
that sufficient space between the
steel or other
reinforcement and the edges of the
mould or formwork
is left so that there will be enough
concrete
"cover to steel" to
inhibit rusting.
-
Before
use, cover all form or mould faces
in contact with the concrete
with a recognised release agent as
thinly, but as thoroughly,
as possible to assist in securing a
clean release without
damage to the concrete, or to the
mould or shutter.
-
NB
- Avoid
getting release agent on
reinforcing bars - this
will stop
them bonding with
the
concrete.
-
Before
placing concrete in foundations, or
against earth
or other materials which may draw
water from the fresh mix, wet
the area thoroughly, but not so much
that there is free water standing
where the concrete
is placed.
-
Deposit
concrete as near as possible to its
final position,
in layers (not more than 150 mm
thick for hand compaction, or more
than 450 mm thick for poker
vibration).
-
Air
becomes trapped in fresh concrete
during placing.
To ensure that the concrete attains
its full potential strength,
as much of this trapped air as possible
must be expelled. Pay special
attention to
compacting the edges of slabs,
corners of paving,
etc.
-
When
hand
compacting:
-
As
soon as the first layer has been
placed, rod, spade and/ or tamp
the concrete, taking care to work
the concrete well against formwork,
into corners and around any
reinforcement.
-
Level
and compact slabs such as floors with
a heavy wooden beam fitted with a handle
at each end. Use a chopping action
first, then a sawing motion to strike
off the surface flush with the side
forms.
-
On
thin slabs use a pipe roller to compact
the concrete and finish the surface
in one operation.
-
Compaction
by vibration (This
is usually done with immersion or
poker vibrators)
-
Do
not use the vibrator to move the
concrete from the point of deposit
to its final position as this can
cause segregation.
-
Place
concrete in shallow layers (no more than
450 mm), which must be vibrated
before subsequent
layers are placed.
-
Insert
the vibrator at points close enough together
to allow complete compaction.
-
Insert
the vibrator quickly into
the concrete and withdraw
it slowly.
-
Provide
additional vibration in corners and next
to construction joints.
-
Avoid
touching the formwork with the vibrator.
-
If
cracks develop in the concrete while
it is still plastic, close them up
by reworking or re-compacting the
surface before the concrete sets
-
usually
within three to four hours of
placing.
-
Blowholes
result when air bubbles are trapped
against formwork surfaces
when the fresh concrete is placed
and compacted.
Curing
Newly
cast concrete must be cured to ensure
that hydration continues
until the full potential strength of the
hardened concrete is achieved
and to minimise any tendency to crack.
This means ensuring
that the concrete is kept damp and not
allowed to freeze.
The
more extender in the mix, the slower the
strength development, and
the hardened concrete will only reach
its full potential strength if
it is properly cured.
Concrete
can be cured by:
-
Covering
the surface with a water-retaining
material such as sand, earth, straw
or hessian that is kept continuously
damp.
-
Sprinkling
or spraying with water often enough
to keep the concrete continuously
moist.
-
Ponding
water on the surface.
-
Covering
with plastic sheeting or waterproof paper.
The covering must be held in place at
its edges in a way that does not
damage the
concrete, and be sufficiently
overlapped at
joins.
-
Using
a manufactured spray-on membrane (curing
compound/agent).
-
Leaving
formwork in place and covering any exposed
concrete surfaces.
If
freshly placed concrete is exposed to
hot sunshine
or drying winds, prevent evaporation by
covering with plastic sheeting
immediately after
placing and finishing.
If
the plastic sheeting could damage
the surface, use a water-filled atomizer
spray of the type used
for spraying insecticides on fruit trees
to produce a mist over the
fresh concrete until the surface is hard
enough to permit one of the above
curing methods.
It
may also be necessary to provide
adequate wind breaks for the concrete
during cooler parts of the day. In
cold weather, protect newly placed
concrete from frost by covering
it with an insulating material such as
sacking or straw.
Continue
curing for at least five days after
placing concrete, and
longer
(seven days) in cold weather.
Adequate
curing results in concrete attaining its
potential compressive
strength at 28 days.
|